Melbourne Civil & Structural Engineers can offer you compliance audits for sections 4.1.3 of the Guidelines for school playgrounds. This would form a part of your current School Playground Safety Management Plan.
Section 4.1.3 Audit
A detailed examination (audit) of the entire playground, including all items of play equipment, should be conducted at least once annually.
This audit has three components: assessment, evaluation and rectification.
Assessment- The following aspects of playgrounds should be assessed.
General hazards of all play items:
- Damaged, broken, bent or missing components
- Loose or poorly fitted components
- Excessive wear of components
- Damage to protective coating of components
- Chipped or damaged paint
- Exposed rail or accessory ends that should be protected with caps
- Worn or deformed 'S’ hooks
- Lack of lubrication on moving parts
- Loose fasteners, nuts or bolts
- Sharp or dangerous edges or protruding bolt ends
- Worn, squeaky or 'stiff motion’ bearings
- Perished or damaged rubber components
- Worn swing bearings, swing chains, swing chain mounts, fasteners, or pins
- Remnants of old equipment
- Rust, rot and general deterioration.
Access and platforms:
- Stairways and ladders
- Stepped ladders
- Rungs and handgrips
- Handrails
- Guardrails and protective barriers.
Site conditions:
- Exposed cracked or loose concrete footings
- Worn, scattered or compressed surface material
- Exposed roots, rocks or other environmental obstacles that create potential trip hazards
- Broken glass, refuse or foreign objects around and on play equipment
- Poor drainage areas
- Sloping surfaces
- Trees
- Sandpits.
Zones for equipment:
- Separate play areas by group, type of equipment, and active or passive play
- Adequate spacing between items of equipment
- Adequate space at exit points of slides
- Fall-zones.
Evaluation
The second component of the audit evaluates the results of the assessment with respect to each playground and item of play equipment. Criteria should be established for setting priorities for the rectification of any problems.
The following example of a hazard classification system rates problems as posing high, medium or low risks.
High level of hazard—life or limb threatening hazard, including:
- Falls from heights
- Inadequate impact-absorbing material
- Head or neck entrapment points.
Medium level of hazard—potential injury, but not life threatening, such as:
- Dynamic functions integrated with static items
- Finger, toe and limb entrapment points
- Irregular and extended step distances
- Lack of grab bars on platforms
- Lack of guardrails for dynamic equipment.
Low level of hazard—minor injury potential or does not comply with adopted standard of care, including ground-level activities that usually involve single users such as:
- Rockers
- Roll-over bars
- Climbing apparatus
- Tripping and blind spots
- Unguarded tunnels.
Rectification
The third step of the audit is to renovate, repair or replace any equipment or area with identified hazards. All equipment posing a high level of hazard should be removed from play immediately and replaced or repaired as the first priority. Play equipment evaluated as posing a medium level of hazard should then be repaired or replaced.
We were very happy with the service provided by mcs engineers . They were punctual efficient and thorough . We would not hesitate to recommend this company .
Sandra nowoweiski - Armadale - VIC
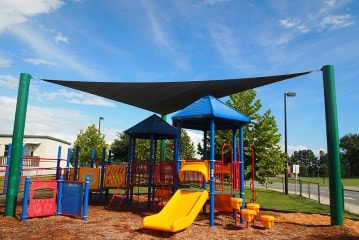